- 2006/04/27 -
The history of Taiwan's plastic extrusion machinery industry can be traced back to four decades ago, and most of the manufacturers in this line today have been around for nearly as long. Over the years, many large-sized manufacturers have steadily upgraded their product lines and now turn out a variety of high-value-added items for customers around the world.
Some manufacturers have made significant strides in developing high-speed and high-efficiency machines that opened doors for them into advanced markets. They also continue to be a force in developing markets, especially in Southeast Asia.
According to the government-backed Plastics Industry Development Center (PIDC), there are over 250 plastic processing machinery manufacturers in Taiwan. Producers of plastic injection-molding machinery account for the biggest segment, with a three-fourths share of total output in Taiwan. Extrusion machine production comes second, accounting for most of the remaining 25%.
According to statistics compiled by the Taiwan Association of Machinery Industry (TAMI), Taiwan exported US$863.756 million worth of plastics and rubber processing machines in the first 11 months of 2005, up 2.5% from US$843.06 million registered in the corresponding period of the previous year. Exports in the segment accounted for 7.2% of the overall exports of Taiwan-made general machinery in the first 11months of last year.
TAMI notes that the top export markets for Taiwan-made plastics and rubber processing machines in the first 11 months of last year were mainland China and Hong Kong, the United States, Japan, Thailand, Vietnam, Malaysia, Indonesia, Turkey, Germany, South Korea, and Canada.
Wang Cheng-ching, vice president of TAMI, says exports of such machines slowed in the said period due to a sharp rise in material prices and the appreciation of the New Taiwan dollar against the U.S. greenback.
Priced to Sell
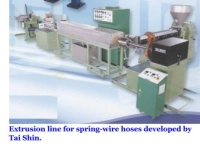
Tai Shin Plastic Machinery Co., Ltd. Is one of Taiwan's most veteran manufacturers of extrusion lines and palletizing equipment. Since its inception, the company has concentrated on rolling out price-competitive machines rather than on constant expansion of output capacity and product lines.
The company's main product lines include extrusion lines for flexible hoses enhanced with spiral yarn inserts, PVC (polyvinyl chloride) palletizing lines, co-extrusion lines for soft/rigid spiral-wound pipes, twin-screw extrusion lines for PVC pipes and profiles, and extrusion lines for spring-wire hoses.
The company's co-extrusion line for pipes is capable of producing soft/rigid spiral-wound pipes with two-inch inner diameters. "Each machine is capable of rolling out 1.5 meters of plastic pipes per minute, three times more than competing models produced by other domestic manufacturers, " says Tai Shin general manager Gordon Chang.
To ensure high product quality, the company imports top-grade key parts and components from industrially advanced nations. The company has an in-house R&D department capable of developing innovative products, including a unique extrusion line for spring-wire hoses. "The line is capable of producing fracture-free one-piece spring-wire enhanced hoses, " he states.
At present the company exports 90% of its overall output, with major markets including Brazil, Argentina, Egypt, the Middle East, and Southeast Asia.
Chang says his company is not interested in expanding simply for the sake of expanding, but will continue to focus on producing high-quality machines.
Innovating Up
With more than three decades of production experience, Chi Chang Machinery Enterprise Co. is one of Taiwan's leading manufactures of plastic-extrusion machinery.
Since its establishment the firm has focused on developing innovative products through its in-house research and development department. The company claims to devote a large part of its annual revenue to design machines meeting the demanding needs of customers in industrially advanced countries.
At present, the company's main product lines include air bubble sheet co-extrusion lines, multi-layer sheet extrusion lines, PS/PE (polystyrene/polyester) foam sheet extrusion lines, PP/PC (polypropylene/polycarbonate) hollow profile sheet extrusion lines, and automatic cast PE extrusion lines for making breathable film for baby diapers.
Chi Chang claims to be the first company in Taiwan to commercialize the production of EPS (expanded polystyrene) sheet making machines, HDPE (high-density PE) mono-axial stretching blown machines, PP hollow profile sheet machines, and PVC (polyvinyl chloride) foamed sheet making machines.
Other major products in the company's well-developed product lines include co-extrusion single/double station blow molding machines with view strips, expanded PVC pipes extrusion lines, extrusion system lamination machines, rigid PVC/PE pipe making machines, PVC compounding palletizing equipment, auto blow molding equipment, PVC garden hose making machines, and PVC reinforced hose making machines.
Two and a half years ago the company led the local field in debuting its expanded PS plank extrusion line with such features as heat insulation, waterproofing, compression resistance, and easy operation. This production line consists of a five-station automatic loading system, plank extrusion line, and automatic packaging machines.
In addition to single-unit machines, the company also offers complete and turnkey projects. Chi Chang can help customers install complete production lines, it says, handling all processes from plant design and layout through production.
The company has been exporting its products since 1980. Its main overseas markets today include the United Kingdom, Russia, Belarus, Australia, Japan, Canada, and the United States.
Global Reach
Another well-noted manufacturer in the plastic extrusion machinery line is Fong Kee Iron Works Co., Ltd. Thanks to its dedication to developing innovative high-end machines, the 53-year-old company has secured a good reputation at home and abroad.
Fong Kee has a solid in-house research and development team and a global sales network to provide integrated technical support and high quality service. The company has regional agents in Greece, Britain, Germany, and Italy.
The company says its products can compete in terms of quality with those made by the highly industrialized nations because of its long-term efforts to develop cutting-edge technologies. The company's products have been marketed to 97 nations around the world.
Fong Kee recently introduced a new PP plate extrusion machine to meet demand from the Indonesian market. With a capacity reaching up to 800kg per hour, the machine can compete with similar models produced in Europe and the U.S.
Wei Chan-wen, president of Fong Kee, says his company has developed five types of machines. Over 90% of the company's total output is exported. To diffuse operating risks, the company has been making all-out efforts over the past several years to diversify its export markets. The result has been a growing presence for the company in such markets as Eastern Europe, Latin America, and Southeast Asia.
Huang Bai-chang, Fong Kee's deputy general manager, notes his company has steadily enhanced the performance of its products. The company's new 150mm extrusion machine equipped with a 400hp motor and imported gear pump can slice one roll into two. The machine's rewind table has also been adapted to handle 1.5mm rolls. The new machine increases productivity while saving space and reducing power consumption and labor costs, all of which add up to greater profitability for customers.
At the end of last year, the company introduced a new blow molding machine for RO reverse pervasion pressure containers. The container is molded in the shape of torpedo and is used in the RO reverse pervasion bucket for drinking water. Thanks to its reliable quality, the product has generated a strong demand among top reverse pervasion equipment manufacturers in the U.S.
Blow molding machines can also be used for making large plastic components like tabletops and chairs. German companies formerly dominated the manufacturing of machinery to make these components, but Fong Kee recently developed a competing machine that matches international standards. Fong Kee has also developed new technology to create a single-head double-mold blow-molding machine. The machine is based on the principle of co-extrusion and can be used to make chemical containers in a cost-effective way.
To serve the expanding market for plastic extrusion machines, in recent months Fong Kee has expanded its production facility by 242.4 square meters and is increasing the number of its employees to expand production capacity. The company expects the expansion to enable a 40-50% growth in sales this year.
Plastic Extrusion Pioneer
Founded in 1963, Intype Enterprise Co., Ltd. (formerly known as Tung Tai Machine Works) is one of the pioneer manufacturers of plastic extrusion machines in Taiwan.
Intype is located in Tainan City, southern Taiwan, where the majority of the island's firms specializing in the production of plastics processing machines, including plastic injection molding machines, are congregated. The right production site has helped the company deeply look into the real demand of the plastics processing sector.
Intype is one of the founders of Taiwan's domestic plastic machinery industry. According to general manager Johnny Chou, the company has accumulated a great deal of experience in developing state-of-the-art automated plastic injection molding machines to meet the special requirements of customers from around the world.
"In light of labor shortages that have occurred in the past several years, more and more manufactures have demanded automated machines that can be operated with fewer hands while simultaneously boosting output of standardized products, " comments Chou. "That's why we have been focusing on the elevation of core technologies to help customers boost factory automation. Our machines can provide a total solution for our customers' needs."
Intype is capable of providing turnkey production facilities, including planning, design, automated material conveying systems, and labor-saving machines.
Thanks to its efforts to develop automated machines, the ISO-9001 and CE-certified company has succeeded in expanding sales worldwide, especially in Southeast Asian nations, Europe, and the U.S.
At present, the company's major product lines include high-performance single/twin-screw extrusion for compounding and master batch pelletizing machines, underwater pelletizer systems, single/twin-screw extrusion machines for plastic profile materials, twin-screw extrusion plastic pipe making machines, and single/screw extrusion for PP (polypropylene) tubular film blowing making machines.
"We have recruited many high-caliber people with expertise in developing computer graphics and automated mechanical services to meet the needs of global customers, " says Chou.
Chou says that the plastic injection molding machine sector has become more competitive in recent years with the entry of several newcomers. To reduce the impact of the price competition and secure the confidence of customers from around the world in the years to come, Chou says that his company will devote more efforts to developing innovative products while simultaneously focusing on providing high-quality after-sale services. Intype will also employ an ERP (enterprise resource planning) system to assist it in developing higher-quality machinery and boosting operating efficiency.
Broad Range
Founded in the early 1980s, Jenn Chong Plastics Machinery Works Co., Ltd. Is recognized as a prominent manufacturer of high-quality extrusion lines for the plastic industry globally.
Jenn Chong has developed a wide range of plastic extrusion lines to facilitate the specific needs of customers from around the world. Its product lines range from complete blown film extrusion system for single- or multi-layer film, monofilament extrusion lines, flat-yarn making machine, fibrillated yarn making machine, extruded net making machine, and strapping brand making machine, to plastic extruding machines, including whole-plant equipment for plastic bags and woven bags on the turnkey basis.
Every Jenn Chong extrusion line is manufactured in compliance with major international standards. The company says it obtained ISO9002 certification in 1998, ISO9001 certification in 2000, and CE mark in 2004, ensuring the high quality and reliability of its products.
Jenn Chong says that over the past several years Jenn Chong has been making all-out efforts to develop advanced manufacturing technologies.
Jenn Chong has an in-house R&D department in charge of developing innovative products. "Thanks to the dedications of the R&D unit, we are very proud of our ability to supply high-quality extruding lines that have won our customers' great confidence, " says James Huang, export manager of the company. At present the company has more than 500 customers in over 70 nations worldwide.
The company says that it is adept at responding rapidly to the fast-changing demands of customers around the world.
In recent years, Jenn Chong has been developing and improving monofilament and multifilament machines. The company's monofilament extruders are suitable for making PP/PE, PVC, nylon (PA6, 66, 6/66 copolymer) and PET for various industrial applications. The company has also enhanced its multifilament spin draw plants for UDY, POY to FDY from simple two-end/one-position models to more complex 32-end/eight-position spinneret beams.